Pellet stoves, especially models like the Pelpro PP130, have gained popularity for their efficiency, eco-friendliness, and cost-effectiveness in heating homes.
But like any appliance, the Pelpro PP130 isn’t without its quirks. In this article, we’ll discuss the common problems that users encounter with the Pelpro PP130 and provide step-by-step solutions to fix them.
How the Pelpro PP130 Works
To understand the issues, it’s crucial to grasp how the Pelpro PP130 pellet stove operates. Pellet stoves use compressed wood pellets as fuel. The stove’s auger system feeds these pellets into a burn pot, where they are ignited to produce heat.
A blower distributes the warmth, making it a highly efficient heating system. The Pelpro PP130 model is known for its large hopper, long burn time, and relatively easy maintenance.
PP70 Pellet Stove: 70 lb Hopper, 42,500 BTU Heats up to 2,000 Sq. Ft
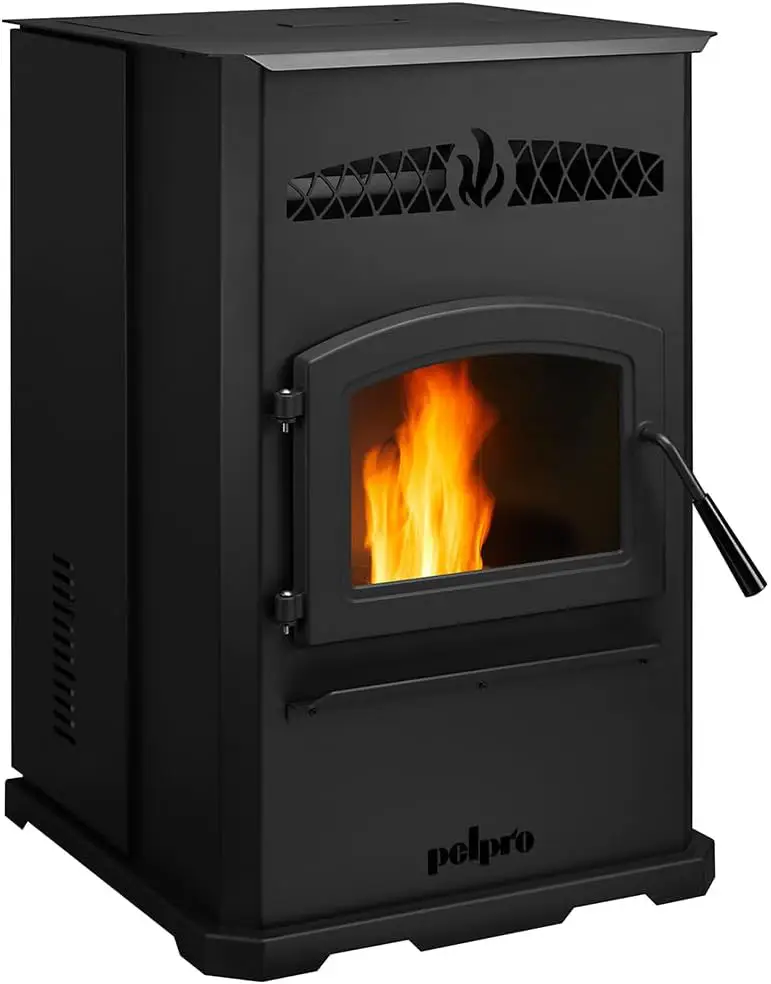
- Heats up to 2,000 sq. ft. with 42,500 BTUs.
- EPA-certified efficiency for fuel savings.
- 70-lb. hopper holds 2 days of pellets.
- 10 heat settings with quiet blower and thermostat.
- 300W auto-igniter for easy start.
Common Issues with the Pelpro PP130 Pellet Stove
Issue 1: Pellet Stove Not Igniting
One of the most frequent complaints from Pelpro PP130 users is that the stove fails to ignite. There are several reasons for this, such as a faulty igniter, poor airflow, or damp pellets.
Fix for Ignition Issues
- Clean the Igniter: Over time, soot and ash can build up around the igniter, preventing it from reaching the necessary temperature to light the pellets. Clean the igniter with a brush or compressed air.
- Check Airflow: Ensure that there’s proper airflow in the combustion chamber. Blocked vents or an exhaust full of ash will hinder ignition.
- Inspect Pellet Quality: Always use dry, high-quality pellets. Damp or low-grade pellets may not ignite easily.
Issue 2: Poor Pellet Feed or Jammed Auger
Another issue you might encounter is that the pellets don’t feed properly into the burn pot, often because the auger is jammed or malfunctioning.
Fix for Pellet Feed Problems
- Clear the Auger: Unplug the stove and clean out any jammed pellets from the auger. Pellets can sometimes get stuck, especially if they’re slightly oversized or damp.
- Adjust Feed Rate Settings: The Pelpro PP130 pellet stove has adjustable feed rates. Make sure you’re using the correct setting for your desired heat output. Too slow a feed may lead to insufficient pellets for combustion.
- Dry and High-Quality Pellets: Wet or crumbly pellets often cause jams. Make sure to use pellets that are stored in a dry location to avoid issues.
Issue 3: Pelpro PP130 Overheating
Overheating can be a serious problem, as it may cause damage to the stove or even create a fire hazard. It’s usually caused by improper airflow, dirty components, or incorrect thermostat settings.
Fix for Overheating Problems
- Adjust Thermostat Settings: Sometimes, the stove might overheat if the thermostat is set too high. Try lowering it and see if the stove stabilizes.
- Clean Heat Exchanger and Vents: A dirty heat exchanger can reduce the stove’s ability to regulate its temperature. Ensure the heat exchanger and venting system are free of soot and ash buildup.
Issue 4: Low Heat Output
If your Pelpro PP130 is running but not producing enough heat, there could be several causes, such as poor combustion, blocked airflow, or improper settings.
Fix for Low Heat Output
- Adjust Airflow and Damper Settings: Check that the damper is adjusted correctly. Too little airflow will result in poor combustion, reducing heat output.
- Ensure Optimal Pellet Feed: Make sure the feed rate is set correctly so that enough pellets are being delivered to the burn pot for a strong flame.
Issue 5: Stove Shutting Down Unexpectedly
Does your stove randomly shut off? This can be both frustrating and concerning. It’s often due to sensors detecting a problem, such as overheating or airflow issues, or a malfunction in the control board.
Fix for Sudden Shutdowns
- Clean Sensors and Exhaust Vents: Many pellet stoves, including the Pelpro PP130, have sensors that detect blockages or overheating. Ensure these sensors are clean and functioning properly.
- Check for Sensor Malfunctions: Sometimes, the sensors themselves may fail. If cleaning doesn’t help, it might be time to replace them.
You May Also Like To Read:
FAQs
Why isn’t my Pelpro PP130 igniting?
The most common reasons include a dirty igniter, blocked airflow, or low-quality pellets. Cleaning and inspecting these components can help solve the issue.
How often should I clean my pellet stove?
It’s recommended to clean your stove after every 1-2 bags of pellets and do a deep clean at least once a month during heavy use.
What kind of pellets should I use with the Pelpro PP130?
Use high-quality hardwood pellets, as they burn cleaner and more efficiently than lower-grade or damp pellets.
How do I prevent my stove from overheating?
Regularly clean the heat exchanger and exhaust vents, and make sure the thermostat settings are appropriate for your desired room temperature.
Why does my stove keep turning off unexpectedly?
The issue could be due to clogged vents or malfunctioning sensors. Cleaning the sensors and ensuring proper airflow can help solve this problem.
Affiliate Disclosure: Fireplaceadviser.com is a participant in the Amazon Services LLC Associates Program. We may earn a commission when you click on certain links on this site and purchase.
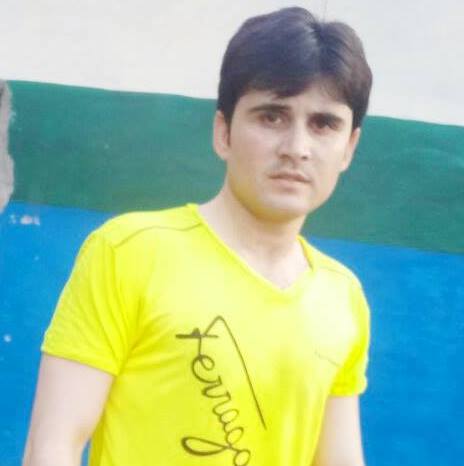
Hello!! I am Jamal Khan. I often fix my home electric heaters and gas stove problems and research the common issues in the heating units to improve my knowledge and expertise. The aim of establishing fireplaceadviser.com is to share my expertise and knowledge with my audience.
Why is my pelpro PP130 making a rattling sound when shutting down. I have replaced both the exhaust blower and the convection blower
Hello Gordon,
Thanks for approching us. A rattling sound in your Pelpro PP130 when shutting down can be attributed to several factors, even after replacing both the exhaust and convection blowers. One common cause is vibration from the convection blower, which can resonate through the stove’s metal components, creating a rattling noise.
This vibration may be exacerbated by loose or poorly secured parts, such as the blower housing or mounting brackets, leading to increased noise during shutdown as the stove cools and the fans slow down.
Another potential issue could be related to the stove’s control board or settings. If the shutdown sequence is not functioning properly, it might cause irregular fan operation, contributing to rattling sounds. Ensuring that all electrical connections are secure and that the control board is functioning correctly is essential.
Additionally, accumulated ash or debris in the blower housing or exhaust system can lead to noise; therefore, regular cleaning and maintenance are crucial for optimal performance and noise reduction.
If these steps do not resolve the issue, further inspection may be necessary to check for any mechanical failures or misalignments within the stove that could be causing the rattling sound during shutdown.
my fuse on my curcuit board on my pel pro130 pellet stove keep blowing
It sounds like your Pel Pro 130 is having an electrical issue. A fuse blowing repeatedly usually means there’s a short or an overloaded circuit somewhere. Here are a few things you can check:
1. Inspect all wiring and connections – Look for any damaged, loose, or pinched wires, especially around the auger motor, combustion blower, and igniter.
2. Check the components drawing power – A failing motor, igniter, or control board can cause an overcurrent and blow the fuse. If one of these parts is starting to fail, it could be pulling too much amperage.
3. Use the correct fuse rating – Make sure you’re replacing the fuse with the exact type and rating recommended by Pel Pro. A lower-rated fuse will blow even under normal conditions.
4. Moisture or debris – Dust buildup or moisture on the circuit board can cause short circuits. A careful cleaning might help.
If you’ve checked these and the fuse still blows, it’s best to call a qualified technician or Pel Pro customer support. Electrical issues can worsen if left unresolved, and working on a control board can be risky if you’re not familiar with it.